Case Study: P&M Steel
Faster Deadlines Require Faster Production
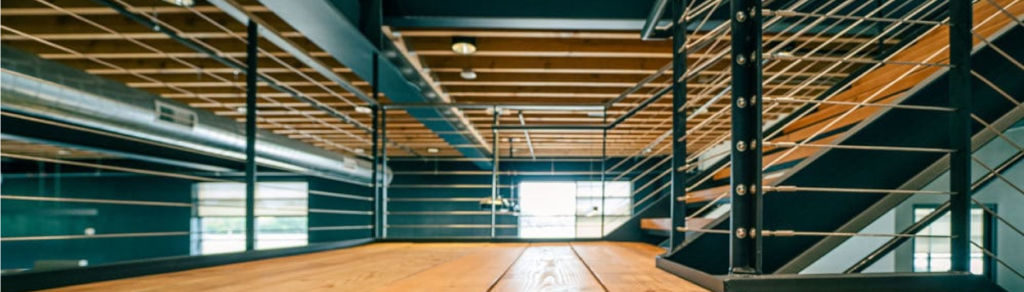
About
P&M Steel focuses on structural steel, fabricating, and miscellaneous metals. Since 1970, they have grown to a volume of 6,000-7,000 tons worth of jobs per year; with work varying from 400-ton jobs to walk-in customers.
Tighter Deadlines
Cutting, notching, and laying out handrails was a manual and time-consuming method that made P&M Steel completely reliant on the fabricator. Facing increasingly tighter deadlines, its slow, manual methods had created a bottleneck in production. The company realized it needed a better solution for tube and pipe fabrication to reduce lead times and meet growing demand.
Dragon A400
To A400 proved to be the perfect solution to improve P&M Steel’s production times. Designed for versatility, the A400 works with a wide range of material types, shapes, and thicknesses. And with the ability to cut, mark, engrave, and align with one machine, P&M Steel could bring any CAD/CAM design to life.
The A400 reduced labor time by over 42% and has cut production time in half. The ability to produce everything accurately with the slot and tab feature has been a game-changer, as railing parts fit together perfectly. The bend marks option allows for correct bends every time. Instead of wasting time drawing each part, detailers can auto-import designs with the Tekla Plugin.
Profitability of the Dragon
The A400 paid for itself in less than two months and has allowed P&M Steel to generate extra income-producing parts for other fabrication companies.