Case Study: Grunau Metals
Eliminating a Production Bottleneck
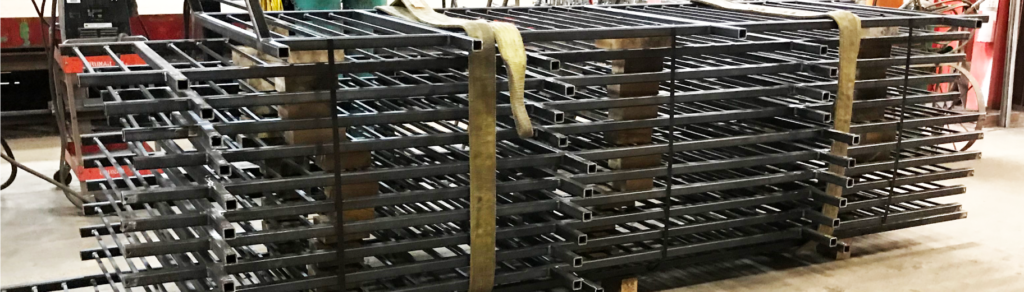
About Grunau Metals
Established in 1920, Grunau Company strives to build positive, long-lasting relationships for industries such as handrails, catwalks, ornamental metals, stairs, wind tunnel caging, and more. In early 2019, Grunau purchased the Bend-Tech Dragon A400 in an effort to continue its 100-year journey in providing quality solutions to its customers. We had a conversation with Justin, the shop foreman at Grunau, to learn about the impact of the Bend-Tech Dragon A400 on tube processing – mostly, for handrail.
Manual Production and Outsourcing
Historically, Grunau processed tube/pipe by traditional methods. Justin said, “We used to saw cut straight bevels and miters. Tubes 1 to 3 inches OD were hand coped. For years the production of stairs and stringers was relatively slow until a new stringer production process increased efficiency. This meant that the slow manual coping and notching methods for 15 to 45 degree angles started to create a bottleneck in the handrail production.” Outsourcing the handrail part production led to issues as well. Among these issues were lead times of 4 to 5 weeks for 50 sticks worth of parts. “The outsourcing company could not use .STEP or .DXF files, which meant that projects had to be recreated entirely by the outsourcing company: leading to increased human error in calculations.”
CNC Plasma Cutting
In early 2019, Grunau purchased a Dragon A400 for processing round and square 1.5 inch to 3 inch materials in an effort to eliminate the slow manual coping process. By returning to in-house production, now with the Dragon A400, Grunau has been able to increase its throughput by approximately 5 times. Justin stated, “Now it comfortably takes 7 hours [compared to 5-days] to run about 50 sticks of material – this includes importing, changing part names, nesting, running, and grouping parts. The Bend-Tech Dragon’s Software import abilities of Tekla and AutoCAD has lead to consistently accurate parts.” When asked about the payback of the Dragon A400. “The A400 probably paid for itself on the first job when we ran 1000 feet of 2.5 inch pipe through the machine. We just calculated on one job that the Dragon A400 saved us over $7,000 for the galvanizing process in how the machine cut weep holes.” Justin closed his commentary by saying, “This is a machine worth having.”