Case Study: Maximum Service Parts
Quick Turnaround for In-House Production
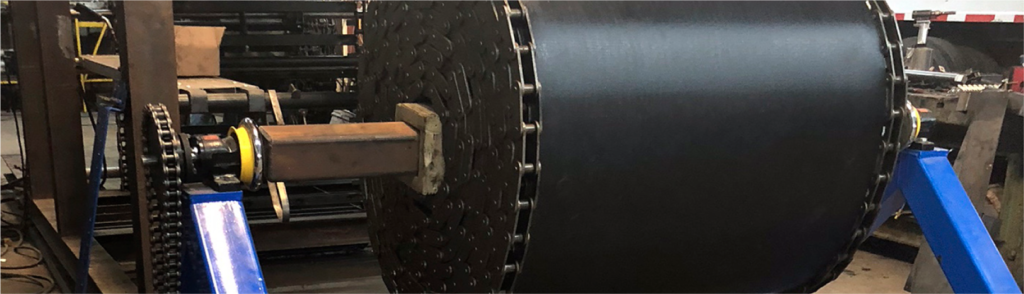
About Maximum Service Parts
Maximum Service Parts specializes in the service and repair for live bottom belt trailers with a quick turnaround time that gets their customers back up and running weeks ahead of the original manufacturer’s timeline. They maintain, repair, and rebuild all brands of live bottom belt trailers, walking floor trailers, continuous belt agriculture trailers, and construction trailers. The original manufacturer’s turnaround time for trailer repair is
typically six or more weeks while Maximum Service Parts produces OEM quality or better, replacement parts and repairs in less than a week in most cases. The quality of their parts and quick service sets Maximum Service Parts ahead of the competition.
Dragon A400
The Dragon A400 helps Maximum Service Parts meet their need for quick turnaround times and high-quality parts. Before the Dragon, parts had to be outsourced or made in-house with less than desirable by-hand methods using bandsaws and grinders. Both options had lead times on tube, angle, and channel parts at about a week. With the Dragon, the lead time is cut down significantly, allowing Maximum Service Parts to provide an even faster turnaround time for the service their customers need. When we discussed the impact of the Dragon A400 with Shane, President of Maximum Service Parts, he stated: “The labor time on parts now cut by the Dragon has been reduced considerably. By hand, it would take 16 hours to make, now it takes 2 hours with the Dragon. The efficiency and speed of the Dragon has increased productivity.”
Quality and Speed
With a unique ability to achieve higher-quality and significantly faster turnaround time, the Dragon A400 has helped Maximum Service Parts solidify their business as a service that sees product out the door in one to two days – a service that is almost impossible for others to match.